Introduction: Forging is a manufacturing process that involves shaping and forming metal through the application of compressive forces. It is a versatile technique used across various industries to create robust and high-quality components. In this article, we will delve into the four main types of forging processes: open-die forging, closed-die forging, impression-die forging, and seamless ring rolling.
- Open-Die Forging: Open-die forging, also known as smith forging or hand forging, is one of the oldest forging techniques. In this process, the metal workpiece is placed between flat or slightly curved dies and hammered repeatedly until the desired shape is achieved. Open-die forging allows for flexibility and versatility in shaping large and complex components with minimal material waste. It is commonly used for producing parts such as shafts, bars, disks, and cylinders.
- Closed-Die Forging: Closed-die forging, also referred to as impression-die forging, involves the use of two or more die halves that contain impressions of the desired component shape. The heated metal workpiece is placed in the die and compressed under high pressure, filling the cavities and acquiring the shape of the die. Closed-die forging offers excellent precision, dimensional accuracy, and repeatability, making it suitable for producing complex parts with tight tolerances, such as gears, connecting rods, and crankshafts.
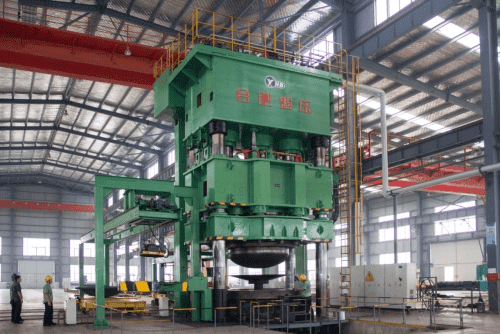
- Impression-Die Forging: Impression-die forging, also known as precision forging or net-shape forging, is a variation of closed-die forging. This process utilizes specially designed dies that impart the desired shape on the workpiece while allowing excess material to flow out. Impression-die forging minimizes the need for secondary machining operations, resulting in near-net-shape components with precise features and reduced material waste. It is commonly employed to manufacture intricate parts, including automotive components, aerospace fittings, and industrial machinery parts.
- Seamless Ring Rolling: Seamless ring rolling is a specialized forging process used primarily to produce seamless rings with high strength and structural integrity. In this technique, a circular metal preform is pierced to create an open-die cavity. The preform is then rolled between two mandrels, applying radial compressive forces that progressively shape the material into a ring. Seamless ring rolling offers superior mechanical properties, such as grain flow and improved fatigue resistance, making it ideal for applications in aerospace, power generation, and bearing manufacturing.
Conclusion: The four main types of forging processes - open-die forging, closed-die forging, impression-die forging, and seamless ring rolling - provide diverse options for shaping and forming metal components. Each process offers unique advantages, such as flexibility, precision, net-shape capability, and enhanced mechanical properties. By understanding these forging techniques, manufacturers can choose the most suitable method for their specific requirements, ensuring the production of high-quality, durable, and accurately shaped components.