What is a Hydraulic Forging Press?
A hydraulic forging press is a machine that uses hydraulic pressure to shape metal. It consists of a hydraulic cylinder that is connected to a ram. The hydraulic fluid is pumped into the cylinder, which forces the ram to move up and down. The ram is attached to a die that is used to shape the metal.
Types of Hydraulic Forging Presses
There are two main types of hydraulic forging presses:
- Mechanical presses use a mechanical linkage to connect the hydraulic cylinder to the ram. This type of press is typically used for smaller forging operations.
- Hydraulic presses use a direct connection between the hydraulic cylinder and the ram. This type of press is typically used for larger forging operations.
Advantages of Hydraulic Forging Presses
Hydraulic forging presses offer a number of advantages over other types of forging presses, including:
- Precision: Hydraulic forging presses can produce very precise forgings.
- Versatility: Hydraulic forging presses can be used to forge a wide variety of metals.
- Speed: Hydraulic forging presses can operate at high speeds.
- Durability: Hydraulic forging presses are very durable and can withstand high levels of force.
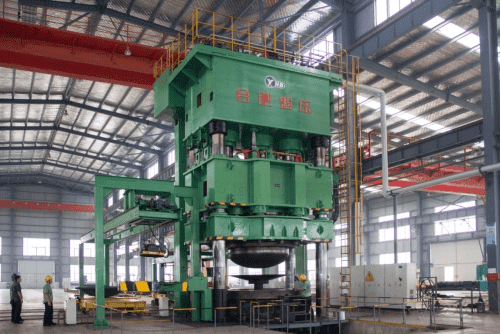
Applications of Hydraulic Forging Presses
Hydraulic forging presses are used in a wide variety of applications, including:
- Automotive: Hydraulic forging presses are used to forge a variety of automotive components, such as crankshafts, connecting rods, and gears.
- Aerospace: Hydraulic forging presses are used to forge a variety of aerospace components, such as aircraft wings, fuselage panels, and engine parts.
- Construction: Hydraulic forging presses are used to forge a variety of construction components, such as beams, girders, and columns.
- Oil and gas: Hydraulic forging presses are used to forge a variety of oil and gas components, such as drill bits, piping, and valves.
6 Most Asked Questions About Hydraulic Forging Presses:
What is the difference between a mechanical press and a hydraulic press?
The main difference between a mechanical press and a hydraulic press lies in the mechanism used to generate the pressing force.
A mechanical press uses a flywheel and a crankshaft to convert rotational motion into the linear motion required for the press stroke, making it suitable for high-speed, high-volume operations.
In contrast, a hydraulic press utilizes hydraulic fluid power to generate the pressing force, allowing it to produce significantly higher forces, making it suitable for applications that require greater tonnage, such as heavy-duty stamping, forging, or deep drawing.
What are the advantages of using a hydraulic forging press?
The key advantages of using a hydraulic forging press include:
High force capacity - Hydraulic presses can generate very high forces for heavy-duty forging operations.
Precise control - The hydraulic system allows for precise control over the forging force and speed.
Versatility - Hydraulic presses can handle a wide range of forging workpiece sizes and materials.
Efficiency - Hydraulic presses are generally more energy-efficient compared to mechanical forging presses.
Consistent quality - The controlled forging process helps ensure consistent quality of the forged parts.
Low maintenance - Hydraulic presses tend to require less maintenance compared to mechanical presses.
What are the applications of hydraulic forging presses?
Hydraulic forging presses are used for forging automotive and aerospace parts, as well as in large-scale industrial component manufacturing.
What are the key considerations when selecting a hydraulic forging press?
When selecing a hydraulic forging press, consider the tonnage capacity, stroke and daylight (the length of the press ram), and platen size to suit the specific forging requirements.
What are the safety precautions that should be taken when operating a hydraulic forging press?
- Proper training
- Wear protective gear
- Use safety guards
- Regular inspections
- Lockouttagout procedures
- Accessible emergency stop
- Overload protection
- Maintain a clean work area
How to maintain a hydraulic forging press?
To maintain a hydraulic forging press, regularly check the oil level, repair leaks, lubricate moving parts, and adhere to the manufacturer's maintenance schedule.
Hydraulic Forging Press Maintenance
Hydraulic forging presses require regular maintenance to ensure optimal performance and safety. Some of the most important maintenance tasks include:
- Checking the hydraulic fluid level
- Changing the hydraulic fluid filter
- Lubricating the moving parts
- Inspecting the dies for wear and tear
- Calibrating the press
Hydraulic Forging Press Safety
Hydraulic forging presses can be dangerous if they are not operated properly. Some of the most important safety precautions that should be taken when operating a hydraulic forging press include:
- Wearing appropriate safety gear
- Keeping the work area clean and clear
- Never putting your hands or fingers in the press
- Being aware of the moving parts
- Following all manufacturer instructions
Benefits of Using a Hydraulic Forging Press
- Increased productivity
- Improved quality of products
- Reduced labor costs
- Reduced material waste
- Increased safety
Considerations When Selecting a Hydraulic Forging Press
There are a number of factors to consider when selecting a hydraulic forging press, including:
- The size and capacity of the press
- The type of metal being forged
- The desired production rate
- The available space
- The budget
Useful Tables
Feature | Mechanical Press | Hydraulic Press |
---|---|---|
Power source | Mechanical | Hydraulic |
Connection between cylinder and ram | Mechanical linkage | Direct connection |
Precision | Lower | Higher |
Versatility | Lower | Higher |
Speed | Lower | Higher |
Durability | Lower | Higher |
Application | Advantages |
---|---|
Automotive | High precision, high speed, low noise |
Aerospace | High precision, high strength, light weight |
Construction | High strength, durability, low cost |
Oil and gas | High strength, durability, corrosion resistance |